Manufacturing New Solutions During the COVID-19 Crisis
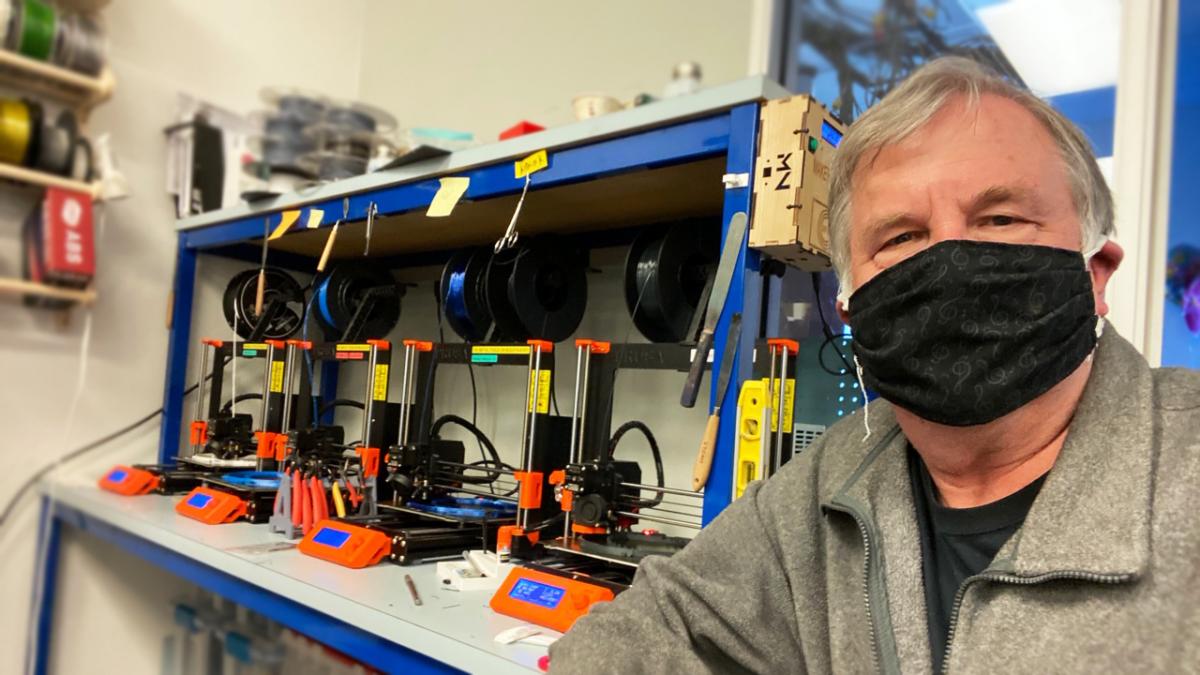
When the COVID-19 crisis began to affect California, Jim Schrempp (Computer Science, ’80) knew he had to do something. Newly retired after working 20 years at Hewlett Packard and then starting his own company, Schrempp had recently become involved in the Bay Area maker community as the VP of the Board of Directors for Maker Nexus. In fact, three of the nonprofit’s six founders have ties to Cal Poly, as well as several others in this 200+ member community. Schrempp and his colleagues recognized that their organization had access to many tools in their 7,000 square foot facility that could potentially be useful in the response to the pandemic. So, when a hospital tweeted they needed face shields and asked if someone in Silicon Valley could help, members of his community brought the idea into their online forums where the idea caught fire, and like other makers around the country, the Maker Nexus community got to work.
“We have three programs running right now at Maker Nexus to help with the COVID crisis,” he said. “We put these programs in place after talking with the Valley Medical Center Foundation. Through them we have been in touch with Kaiser Hospital nurses to review our designs and finished products.”
I don't think I would be doing this if I didn't have my Cal Poly education. Cal Poly really taught me to find the right tool and apply it to the right problem, and to get in there and really get things done the right way."
Jim Schrempp
Computer Science, '80
Using the shop’s 3D printers, they can produce the headbands and plastic parts for face shields that are used by medical teams when dealing with sick patients. “We have six 3D printers of our own working 24 hours a day, and have borrowed nine more from a closed middle school, as well as many more members who are utilizing their own 3D printers at home,” Schrempp said.
They now have over 300 volunteer in-home 3D printers working in their cloud manufacturing group producing parts in various locations, with the eventual goal of producing 1000 masks/day. After the parts are printed, they are dropped off at the shop where the full shields are finalized and assembled. Soon they will be shipping 500 shields to Valley Medical Center, 1000 to Kaiser Hospitals, and 40 to Kindred Hospice, with more to come.
They plan on continuing to make face shields for as long as there's a need and while they have the funds and means to do so. “Hopefully in a few months the normal supply chains will increase their capacity, so we are just trying to meet the need until then. Hospitals and small clinics have told us there are no face shields that can be bought at the moment,” he said. In addition to the face shields, they are also producing face masks and scrubs, and currently have people sewing these at home and dropping them off at their facility for distribution.
Schrempp credits his Learn by Doing ethos with helping him to organize this distributed manufacturing process. “I don't think I would be doing this if I didn't have my Cal Poly education. Cal Poly really taught me to find the right tool and apply it to the right problem, and to get in there and really get things done the right way."